AutoMaster Line
The extensive programme of automatic slicing machines
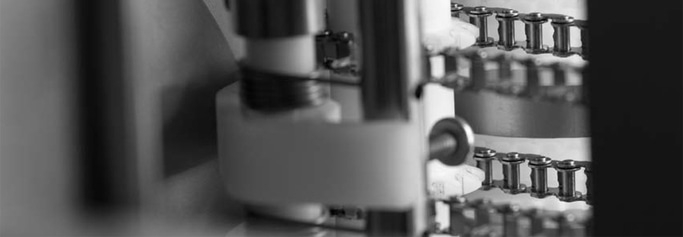
Automatic deposition
Our AutoMaster series stands out for its automatic placer. The unit can be used in the counter areas of butchers, in canteen kitchens, in catering and in industrial production. Excellent cutting and placing results are the basis of the series.
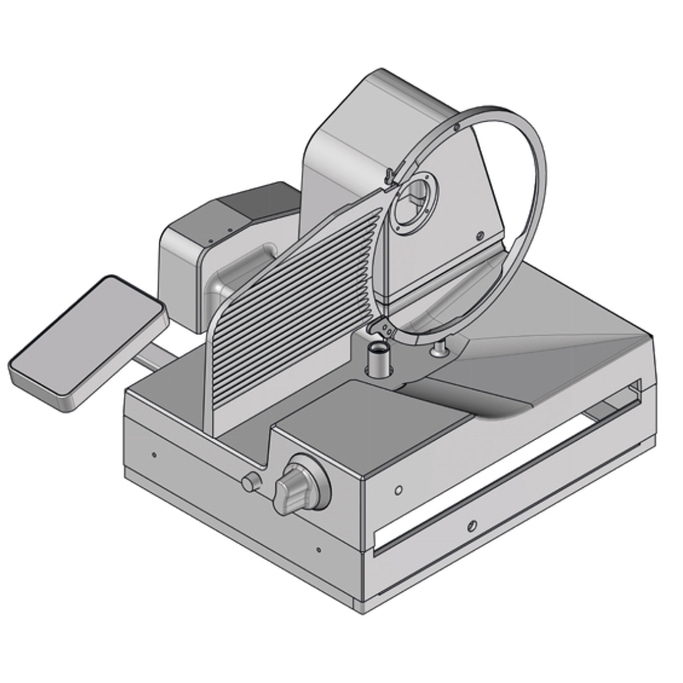
Best slicing results
A double ball-bearing blade transmission in combination with our coated full steel blade guarantees high tractive power and best blade stability. Minimal friction ensured by narrow blade sheaths and a closed blade cover plate.
High-quality ceramic coating
Best gliding properties by high-quality Cera 3 coating and precise guide tracks in stop, blade cover plate and carriage ensure a clean cut. In addition, the cleaning time is reduced considerably.
Maintenance-free motors with air cooling system
Even in case of high load condition over several hours the machine will operate without any problems. The integrated air cooling system ensures cool surfaces and prevents overheating of the motor.
Assortment overview
Semi-automatic .HA
▪ servo-supported manual operation
▪ Carriage removable
▪ Special carriage optionally available
▪ Automatic deposit
Fully-automatic machines .VA
▪ Automatic carriage drive
▪ Automatic material forward feed
▪ Special carriage insert optionally available
▪ Carriage folding down
▪ Deposit tray
▪ Three different carriage lengths
▪ Automatic material forward feed
Fully-automatic machines with conveyor belt .VA FB
▪ Automatic carriage drive
▪ Automatic material forward feed
▪ Carriage folding down
▪ Three different carriage lengths
▪ Interleaving option
▪ Three different conveyor belts
▪ Special carriage insert optionally available
▪ Automatic deposit
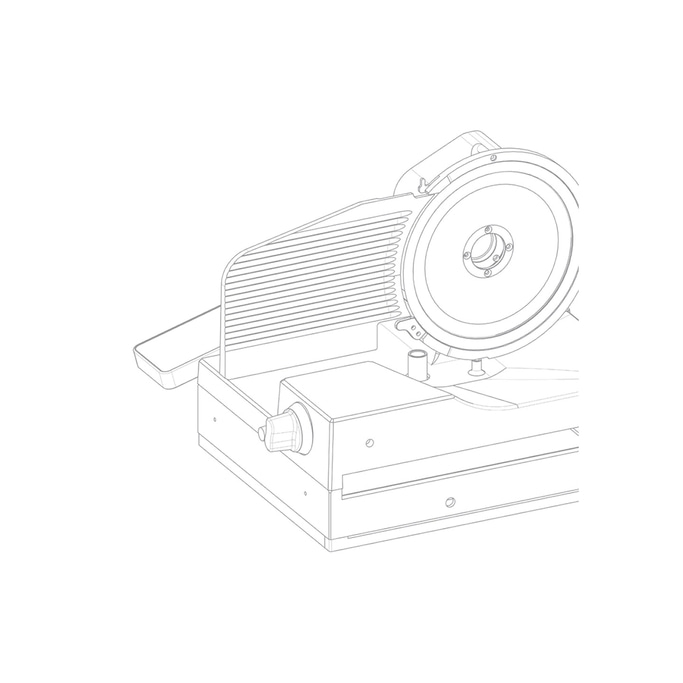
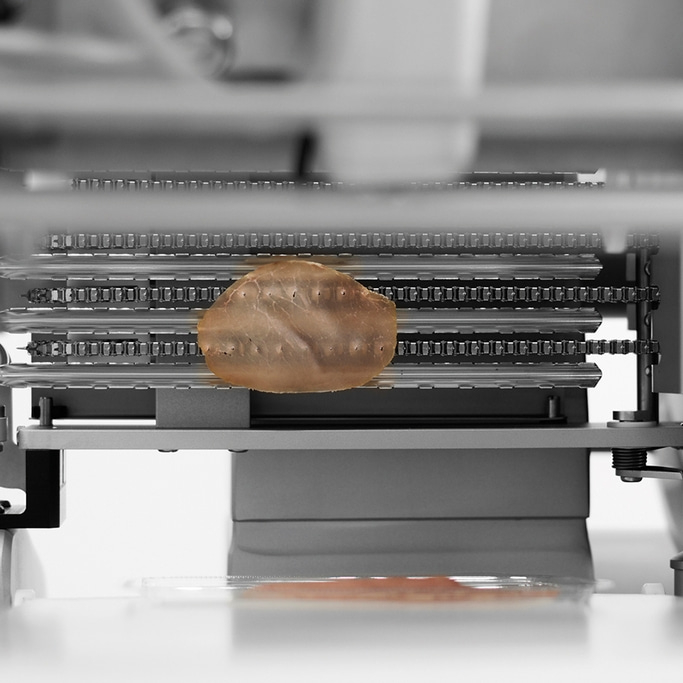
Semi and fully automatic machines
Overview - Common features
Design
- Smooth accessible surface in CERA 3 coating
- Low overall design
- Clearly arranged operating termination, dripping water proof membrane keyboard
- Beater fingers made of stainless special spring steel
- Chain frame with single-part chain links made of stainless steel (patented)
- Chain frame - cheese
- Chain frame - universal
Motor
- Double ball-bearing transmission
- Integrated motor cooling system
- Strong 500 Watts motor
- 230 V or 400 V
Blade
- Smooth solid steel blade with a diameter of 30 cm
- From German production with Cera 3 coating
- Narrow blade sheath
- Closed blade covering plate
Program functions
- Definition of a start programme by keypress
- Modification of the depositing position by keypress
- left - centre - right
- front - centre - rear
- Stack up to four rows
- Stack height - tablet variant 60 mm
- Conveyor belt machine 54 mm
- Selection of the diameter size small - medium - large for circular deposit
- Lengthwise and crosswise deposit up to four rows, variations of the shingle distance
- Round deposit, circular deposit
- Specification of the number of slices
Accessories
- Removable 2-step blade sharpener
- Graef special oil + robust cleaning brush
Technology that works for you
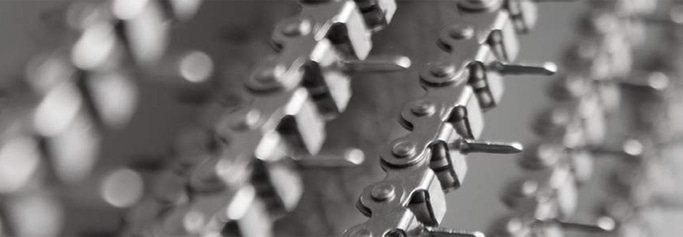
Efficient operation
When it comes to first-class cutting and perfect placing, the AutoMaster Line has all advantages on its side. Innovative technology, high-quality materials as well as an ergonomically well thought out design ensure not only an efficient work employment, but also meet the highest safety requirements.
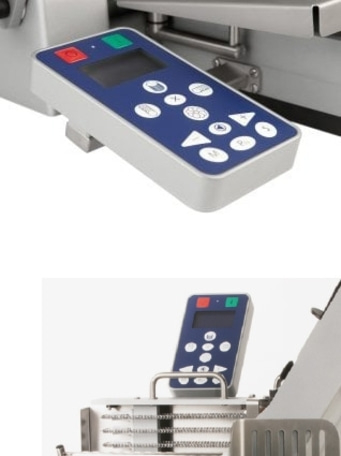
Simple, intuitive operation
The simple intuitive operation of the machine by operating terminal reduces training to a minimum and thus makes the machine operable for everybody. The arrangement on the side can be ergonomically reached. The robust membrane keyboard is dripping water proof.
Operator Terminal can also optionally be placed on top of the machine body.
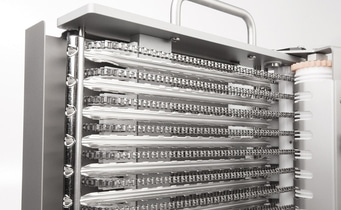
Patented Chain Frame
One-piece chain links with moulded tips made of stainless steel are connected to each other like a bicycle chain. Extremely robust and thus no pre-programmed service costs.
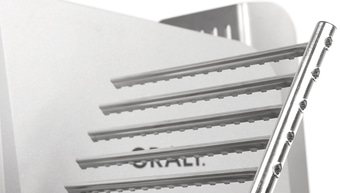
Beater made of special spring steel
The beater deposits the slice transported by the chain on to the tablet or the conveyor belt. The high-quality spring steel makes sure that the beater fingers spring back to their home position. This prevents a collision with the chain. Low service costs, high product availability.

Chain Frame versions
Universal chain frame (standard)
A compromise between sausage and cheese version. Spacing approx. 20 mm.
Cheese chain frame (option)
Ideal for depositing cheese. Spacing approx. 30 mm.
Meat chain frame (option)
Ideal for sausage cuts. Accurate depositing of the product as from a cutting height of 30 mm up to 180 mm. Spacing approx. 10 mm.
Depositing formats - Software
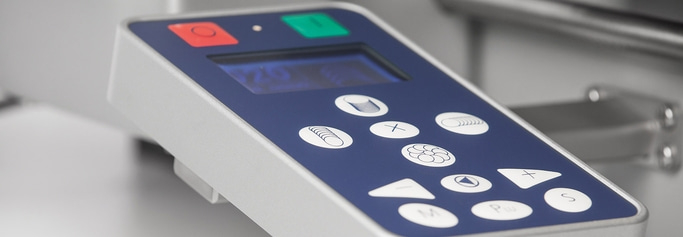
Simple Operation
The start programme and the depositing pattern can be started and varied easily by push off a button. On account of the pre-programmed placing positing and placing diameter, the placing position can be easily changed from left-centre-right or front-centre-rear and the radius can be varied as well. The depositing pattern can also be adapted to your trays or plates.
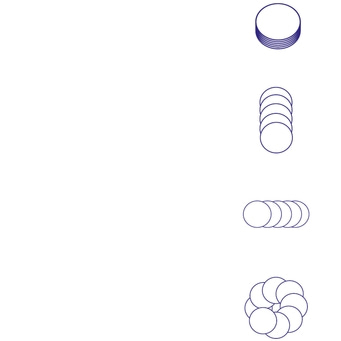
Stacking
Up to four stacks. Maximum stacking height 60 mm
Fanning lengthwise
Up to four rows. Number of slices, depositing position and spacing freely programmable.
Fanning crosswise
Up to four rows. Number of slices, depositing position and spacing freely programmable.
Round deposit
Circular deposit. Radius and number of slices freely programmable.
A new layer
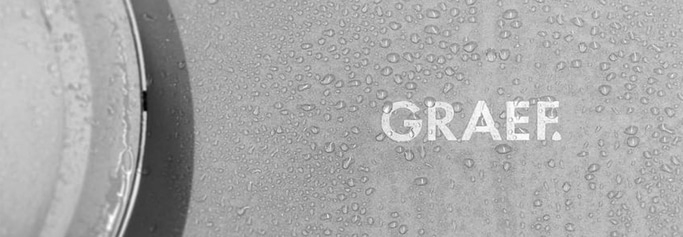
Easy cleaning
The use of anodized aluminium has proved its worth during the last decades as a basis for best cutting resultsand easy working.
Improving good - that is guaranteed by our Cera 3 coating. It facilitates daily work and improves reliability, hygiene and effective handling.
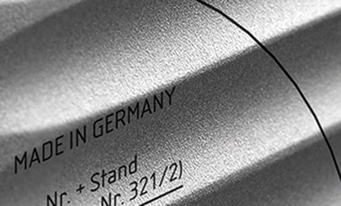
Cera 3 Coating
The new coating is a composition of fine ceramic particles and silicone. It has been developed especially for extremely high abrasion resistance and has been tested in hard industrial use.The new coating is a composition of fine ceramic particles and silicone. It has been developed especially for extremely high abrasion resistance and has been tested in hard industrial use.
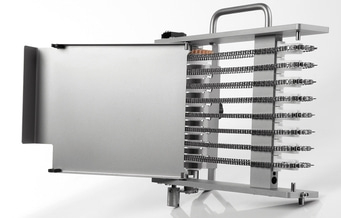
Chain frame cover
The chain cover is closed at the rear. Thus, the motor body is protected against soiling by the cutting material. After removal of the frame, the sheet metal is simply folded down for cleaning.
Cover foldable
High abrasion resistance
The new coating increases the life cycle and is absolutely resistant to corrosion. It increases the value conservation and optical applicability is guaranteed year after year.
Best sliding properties
The ceramic and the share of silicone ensure best sliding properties and prevent sticking of the cutting material. Low-friction and gentle operation
Quick & effective cleaning
As no strong adhesion is possible, you save additional time and reduce the cleaning costs. In addition, the new coating is completely resistant to chemicals.
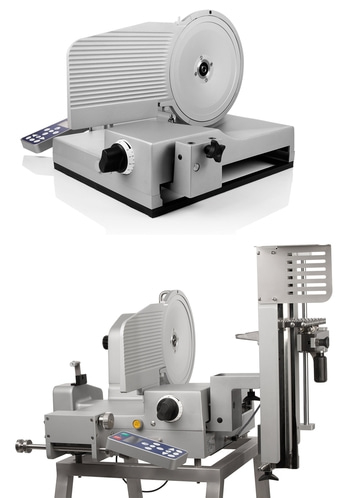
Quick dissassembly
Deposit tray, beater, chain frame and blade cover plate can be removed from the machine quickly and safely. All surfaces are freely accessible and can be cleaned in no time.
The carriage of the HA series can be removed.
The carriage of the VA series can be folded down by 90 degree.
In addition, the the end-piece holder comb of the VA series can be removed easily.
Low overall operating costs
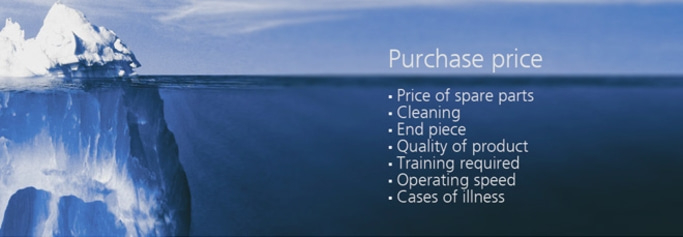
Apart from the visible purchase price, the costs for the overall operating costs not immediately visible are decisive.
Experience and development
During development and realisation, we ensure the use of high-quality materials and make no compromises with respect to the quality of the product. Motors, electronic parts, motor transmission assemblies, films, et cetera are manufactured
in Germany; are subject to a final inspection; and have been designed in such a way that they can stand up to the toughest operating conditions. On account of the innovative and partly patented components, such as the chain frame, pre-programmed service cases are avoided. All this leads to the fact that the costs are low throughout the entire service life of the product and a faster return on investment is ensured.
No pre-programmed costs
The patented chain frame saves service costs as the chains cannot lengthen.
The sample calculation reveals which costs can be saved by a reduction of the cleaning time during 260 production days / year and an assumed minimum wage of € 8.50 (€ 0.14/min. without non-wage costs).
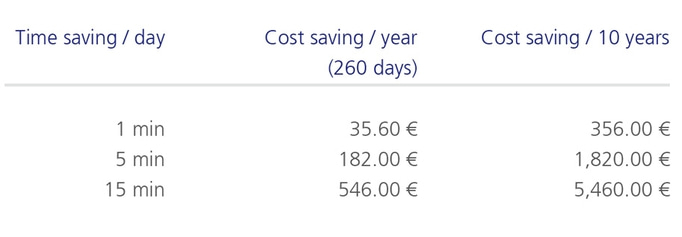
Comparison Table AutoMaster
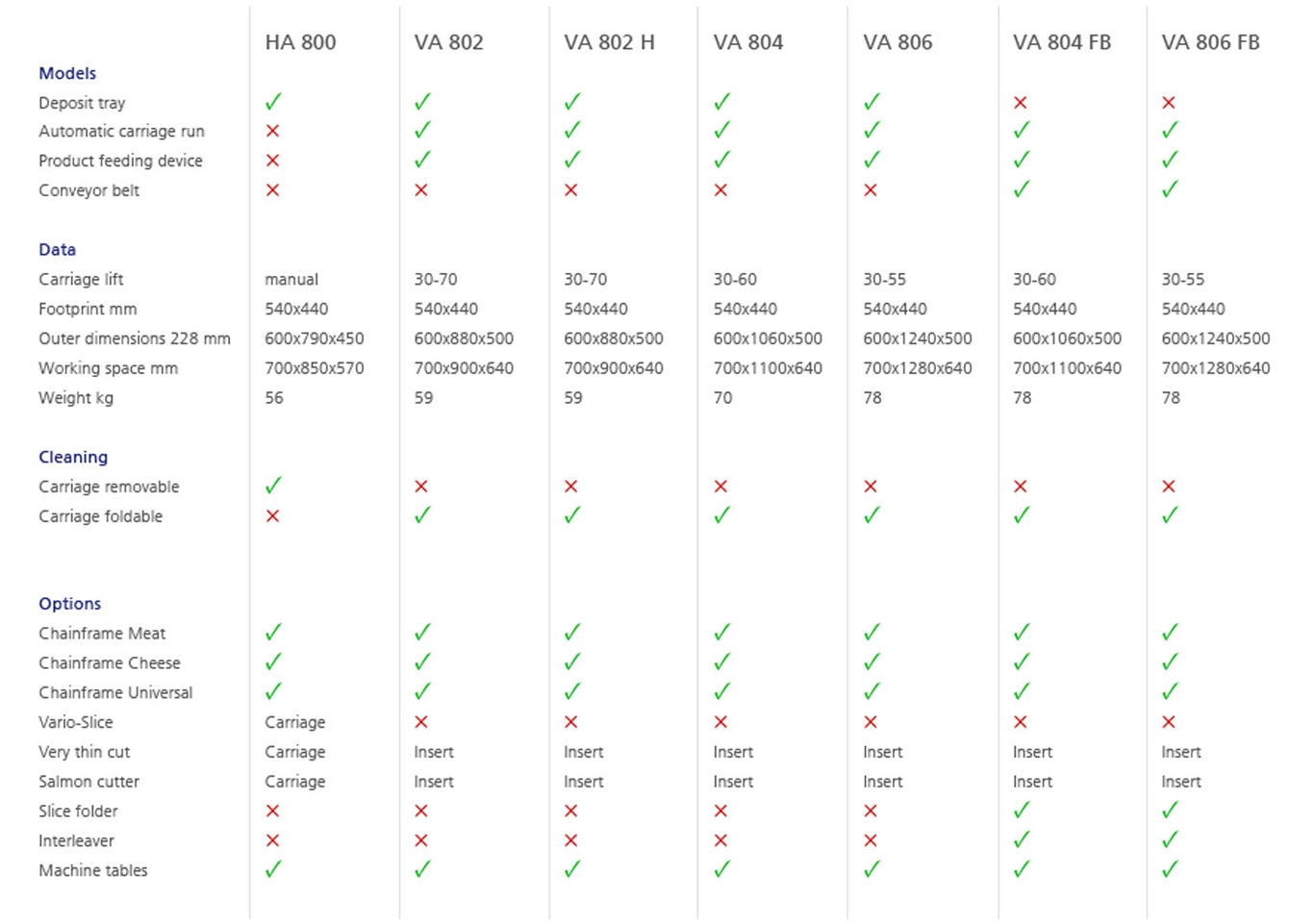